在工業化、規模制造高度發達的今天,制造環節哪怕5%-10%的節約都會被認為是重大進步,成本縮減超過30%?那簡直是顛覆性的。
而知名的復合材料機械制造商Automated Dynamics最近通過3D打印技術的應用,成功地將直升機葉片原型制造過程中的模具成本削減了60%-70%。
Automated Dynamics總部位于紐約的Schenectady。該公司自1984年成立以來,就專注于為高科技、高精密的航空航天、汽車、國防和石油工業提供可靠的復合材料結構。近日,航空航天領域的一位客戶帶著一份緊急訂單找到了Automated Dynamics,要求制造出一個4英尺長的直升機葉片。
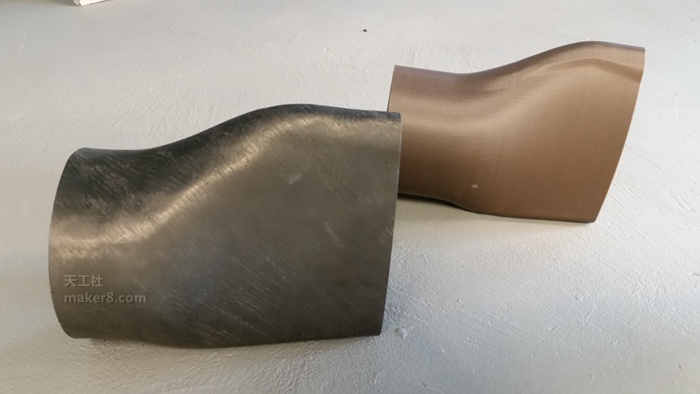
使用FDM技術3D打印的可溶性芯(后面棕色)開發一個4英尺長的直升機葉片,可降低60-70%模具成本
Automated Dynamics公司銷售與市場營銷副總裁Ralph Marcario指出,該公司的工程團隊已經發現,使用傳統的陶瓷或金屬犧牲模板(sacrificial cores)法來制造這類產品導致模具成本非常之高。于是工程師們轉向使用FDM(熔融沉積成型)3D打印技術打造可溶性內核以完成這次直升機葉片的訂單,尋求在降低模具成本的同時也能制造出適度高品質的原型。
“當選擇金屬模具時,往往需要進行大量的工程設計,但是在選擇使用FDM技術制造的模具時,工程師們的設計工作量就變得少了。” Automated Dynamics公司機械設計工程師兼項目經理John Michasiow說。“在某些情況下,金屬模具甚至都不用考慮,我們估計在模具方面的成本節約最少都能達到60%-70%的水平。”
為了制造直升機葉片的模具,Automated Dynamics的團隊找到了Stratasys公司的經銷商CADimensions,由后者在Fortus 400mc 3D制造系統中使用可耐高溫的SR-100可溶性支撐材料3D打印出所需的可溶性芯。在24小時內,該復合成分被Stratasys Direct Manufacturing完全溶解。如果使用金屬模具的話,這些部件的生產周期大約需要六個星期,但是通過使用FDM可溶性芯,整個過程被縮短到大約1周的時間。
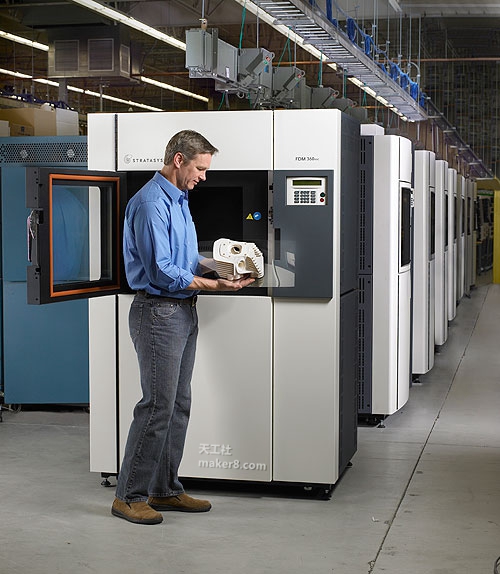
將Stratasys公司的FDM技術應用在可溶性芯模制造中導致了更快的生產時間和成本的削減,避免了可以說是相當困難的去除過程。這一技術可以說逆轉了支撐材料在一般3D打印過程中的作用,在這里熱塑性材料被用于制作支撐模型,而可溶性的支撐材料卻被用來制作芯模。在制造過程中只需簡單地除去熱塑性支撐后暴露出芯模,并用選定的復合材料將其纏繞起來。然后使覆蓋在可溶性芯上的復合材料固化,最后將其浸入水中,使芯模溶解。
通過FDM技術的使用,而不是翻蓋模具(clamshell tooling)和粘接,最終制造出了強度更高的部件,并可以實現更多的幾何形狀,所有這些都在更短的時間里,以一個低得多的成本完成。